Awards and Partnerships
Implementation of Artificial Intelligence in manufacturing processes
Even if the operation’s data is scattered across different sensors, PIMs, and PLCs, Ubivis can collect and centralize production data through our exclusive hardware. The information is centralized and stored in a Big Data infrastructure.
Integrated IoT Solution : With our IoT platform, data from different sources such as mobile devices, desktops, sensors, electrical panels, PIMs, and PLCs can be collected. By eliminating paperwork and digitizing information, it is possible to concatenate and centralize all data related to the manufacturing process. We know that it is common to have data scattered across different platforms and devices. Therefore, it is necessary to centralize and provide agile access to process information.
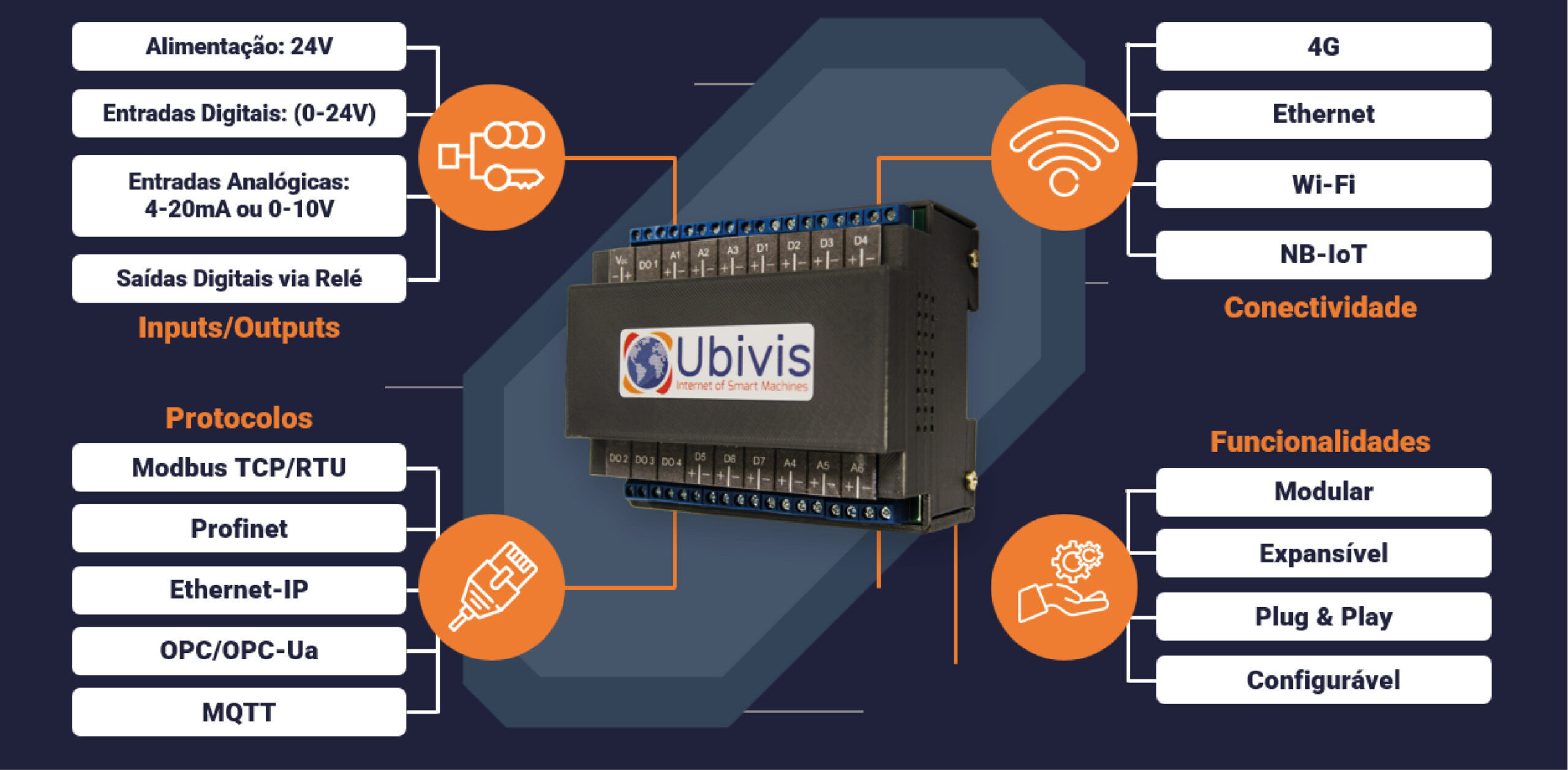
Asset Management via
analytics platforms
We build customized dashboards and Business Intelligence (BI) tools with key performance indicators (KPIs) chosen by the client. We also offer tools for implementing condition-based maintenance with OEE monitoring. Our solution is provided through our exclusive Production Optimization Console.
Asset Management via analytics platforms provides a tool for monitoring asset performance and identifying possible delays and failures in operations. The customizable dashboards offer a detailed view of the data and enable actions to correct the failures. We also offer real-time alarms that notify non-conforming operation parameters, facilitating decision-making by operators.
Some of the key KPIs related to manufacturing operations include:
Overall Equipment Effectiveness (OEE) of a production line from the Production Console Operation system
For maintenance tracking, we also offer Dashboards addressing KPIs such as Mean Time Between Failures (MTBF) and Mean Time To Repair (MTTR).
Ubivis also provides a Correlation Map where statistical similarities between operation parameters can be visualized. Ubivis works with two types of correlation maps.
Trend Analysis / Predictive Maintenance
Trend analysis is important to determine if, and especially when, a critical variable will reach an undesired limit, alerting the responsible party to take precautions before it happens, thus avoiding further losses. It has a significant impact on predictive maintenance, as it can indicate whether, with the current machine operation parameters, the variable or sensor will exceed the ideal operating limits, thereby reducing the equipment's lifespan.
Maintenance for Critical Assets
-
MONITORING
Comparing between historical and real-time asset data
-
KPIs
Conditional performance analysis rules
-
AWARENESS
Identify conditions of occurrence of an active event
-
DASHBOARD
Visual analysis and reports
These are some of the proven results by our clients:
Our Clients
Successful Cases
Contact
